Our Process
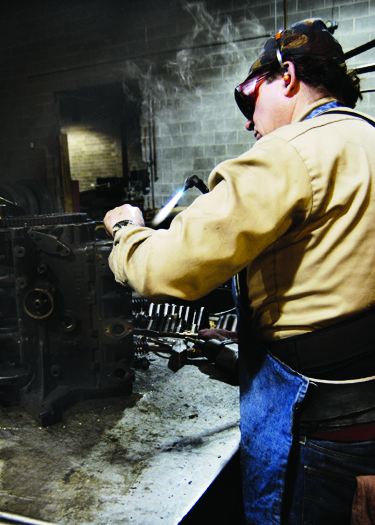
Each engine undergoes a meticulous series of quality control inspections, throughout the remanufacturing process. Before rebuilding we disassemble the engine core, discard the old parts, clean the original castings down to the bare metal, test for cracks, and inspect for defects. We align hone the main bore on the block back to size. Then the cylinders are bored square to the mains and diamond honed. Using a dial bore gauge, we check that each cylinder is round, straight and to size. Our connecting rods are checked for straightness and diamond honed back to factory specifications. Each rod is weighed on a gram scale and put into sets of equal weight.
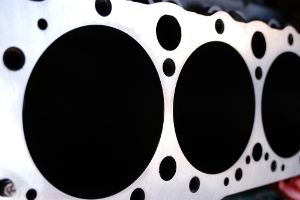
We resurface our cylinder heads to guarantee a good seal. Using the latest technology we tri-cut each valve seat. After assembling the head using new parts, we vacuum test it to ensure a good fit. Crankshafts are checked for straightness and ground to factory specs. We chamfer each oil hole and micro polish the bearing surfaces. Using a profilometer, we check the bearing surface for a perfect finish.
We hand assemble our engines using the finest quality O.E.M. and aftermarket parts available. After assembly, we pressure test the long block to check for leaks. Then we spin test the long block where the cylinder compression, the oil system, and various other quality tests are performed.
This is just a partial list of the many steps taken during the engine building process to ensure you the finest quality engine. Each engine must pass all quality tests before being packaged for shipment.
